What's the PLC and how it used into NC servo feeder?
- Share
- Issue Time
- Nov 14,2019
Summary
PLC system uses a programmable memory for storage in its internal implementation of logical, sequential control, timing, counting and arithmetic operations.
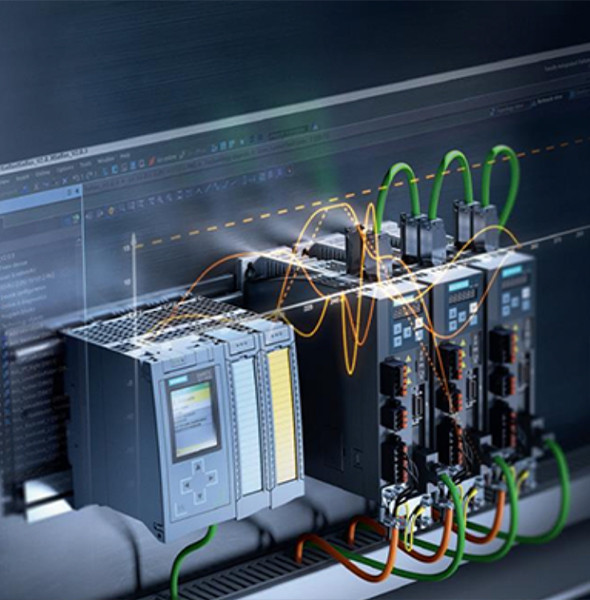
In the field of automation and control, PLC is an important control equipment. Currently, there are over 200 manufacturers of more than 300 varieties of PLC products, applications in the automotive (23%), food processing (16.4%), chemicals / pharmaceuticals (14.6%), metal / mining (11.5%), pulp / paper ( 11.3%) and other industries. In order to make it easier for beginners to understand everybody PLC, the PLC's development this basic structure, configuration, applications and other basic knowledge to make a profile in order to be helpful for you friends.
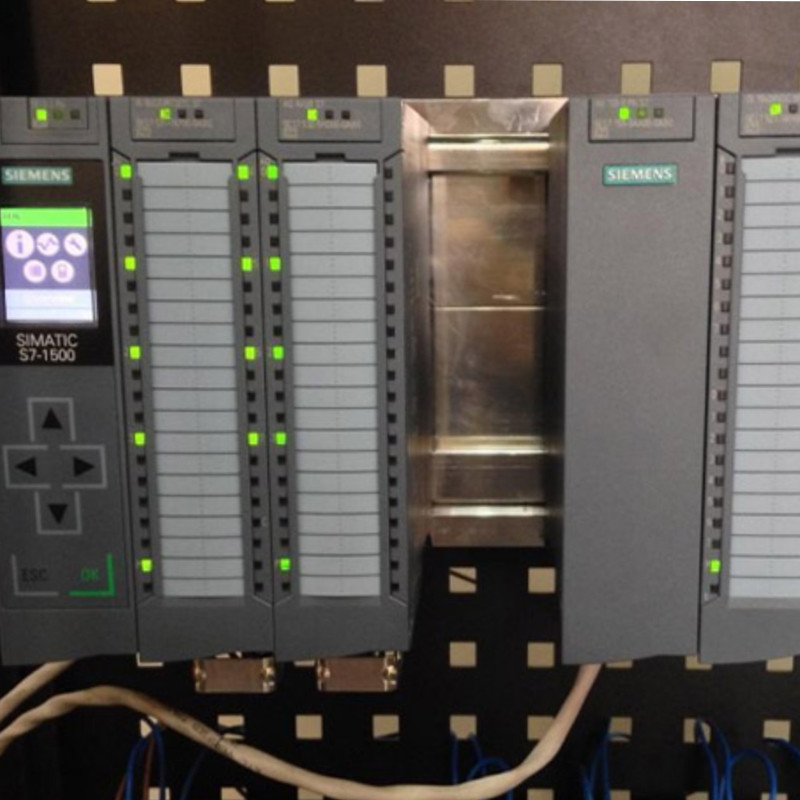
several sequence control switches, which order activities according to logical circumstances and logic chain protection movement control, and several discrete data gathering methods are used in industrial production processes. Traditionally, pneumatic or electric methods have been used to control these functions. In 1968, American General Motors (GM) companies developed a digital integrated circuit and electronics technology based on a control device for the first time using procedural means used in electrical control. This is the first generation of programmable logic controller, known as the Programmable Controller (PC), in response to requirements for replacing the electrical control unit by the second year.The programmable logic controller, also known as the Programmable Logic Controller (PLC), or PC for short, was designed to both facilitate and reflect its functional features. It is still frequently referred to as the PLC PC.
PLC has numerous definitions. The PLC is known as the International Electrotechnical Commission (IEC): An operating system for digital electronic computers intended for use in industrial settings is called a programmable logic controller. Its underlying implementation of logical, sequential control, timing, counting, and arithmetic operations, such as operating instructions, are stored in a programmable memory. It also uses digital and analog inputs and outputs to operate various types of machinery or industrial processes. To further the idea of functional design, programmable logic controllers and associated equipment with industrial control systems should be simple to assemble as a whole.
The fastest rising phase for PLC, with an annual growth rate of 30 to 40%, was from the 1980s to mid-1990s. In this time, PLCs have made significant advancements in their analog processing, number-crunching, man-machine interface, and network capacity. As a result, PLCs have been progressively introduced into the process control domain, sometimes replacing the industry-dominant DCS systems.PLCs are simple to program, very reliable, adaptable, versatile, and have anti-interference capabilities. In the near future, PLCs used in industrial automation and sequence control will not be possible to be replaced.
PLC configuration
PLC separated into two types based on its structure: fixed and modular (modular). The non-removable PLC CPU board is made up of stationary components, an I/O board, a display panel, a memory block, a power supply, and other components. The CPU, I/O, memory, power supply, floor, and rack modules of a modular PLC can be coupled in accordance with predetermined configuration criteria.
CPU composition
The central processing unit (CPU) is the brains behind the PLC; every PLC has at least one CPU. The CPU is assigned by the PLC system program functions to receive and store user programs and data collection methods using a scanning input device sent by the field state or data, and stored in the necessary register, while the PLC detects and reports programming syntax errors and diagnostic power. starts working by reading instructions one at a time from the user program memory. It then generates a corresponding control signal to instruct the control circuit based on the instructions provided by the analysis job.
The CPU unit comprises a peripheral chip bus interface and associated circuitry in addition to the operator, controller, register, and implementation of a data link between them, as well as a control and status bus. Memory is a crucial part of the PLC unit that is mostly utilized to store data and programs.
Important PLC characteristics are PU speed and memory capacity, which govern the PLC's operating speed, IO number, software capacity, etc. and hence restrict the scale's control.
I / O modules
PLC and interface's electrical circuit, via the finished input and output (I/O) section. The PLC I/O circuit is integrated by the I/O module; the output points indicate the output latch's state, and the input signal status registers reflect the input. The output module is the opposite of the input module in terms of digital electrical signals that enter the PLC system. I/O into modules for analog input (AO), digital output (DO), digital input (DI), and other modules.
This indicates that the analog amount is constantly changing, with only the two signal states being switched on and off (or 1 and 0). The following is a classification of common I/O:
Press the 220VAC, 110VAC, and 24VDC voltage level points on the switch.
Relay and transistor isolation are used for isolation.
Analog: There are several types of signals, including voltage (0-10V, 0-5V, 10-10V), current (4-20mA, 0-20mA), and precision points (12bit, 14bit, 16bit, etc.).There are specialized IO modules, such as thermal resistance, thermocouple, pulse, and other modules, in addition to these general purpose IO modules.Press the I/O points to determine the specifications and quantity of the modules. There is no limit to the number of I/O modules that can be managed by the CPU's basic configuration capabilities; the floor or rack can only have a maximum of slots.
Power module
The work for each module's IC power is provided by the PLC power supply. A portion of the input circuit is now providing a 24V power source. AC power (220VAC or 110VAC) and DC power supply (often used for 24VAC) are the two types of power inputs.
Floor or rack
Its functions include electrical, realizing the link between each module so that the CPU can access all the modules on the backplane, machinery, and realizing the connection between each module so that each module becomes a whole. The majority of modular PLCs use a floor or rack.
PLC systems other devices
1. The programming device is an essential tool for developing and implementing PLC programming, as well as for monitoring, operating, inspecting, and maintaining the system. It is used to program the system to adjust certain parameters and to keep an eye on the PLC and its control system's operational state; however, it is not directly involved in field control operations. Small portable programmers are typically used to program PLCs; however, computers running programming software are now often used as programmers.
2. Man-machine interface: The simplest interface is a light and button. The modern integrated operator terminal, which uses an LCD screen or touch screen and is powered by a computer that runs configuration software, is quite common.
3. The input and output devices: these include printers, bar code readers, EPROMs, EEPROM writers, input analog potentiometers, and EPROMs, which are used to store user data permanently.
PLC system applied to NC Servo Feeder
Integrated with smart control systems, enabling automated feeding processes and reducing manual intervention