How to Choose Between Roller Feeder and NC Servo Feeder for Automated Processing ?
- Share
- Issue Time
- Jul 11,2024
Summary
In this detailed guide, we explore the factors to consider when choosing between a roller feeder and an NC servo feeder.
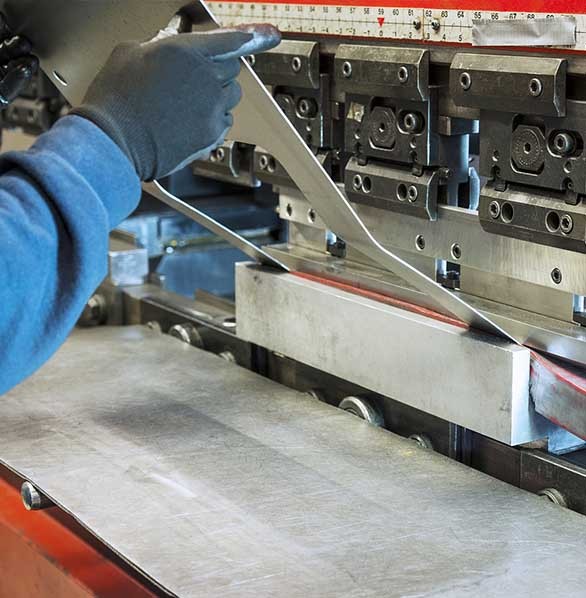
When it comes to automated processing in the manufacturing industry, regarding the press feeder, the choice between a roller feeder and an NC servo feeder can significantly impact the efficiency, accuracy, and overall performance of production operations. Understanding the key differences and advantages of each press feeder type is essential for manufacturers looking to optimize their automated processing workflows. In this detailed guide, we explore the factors to consider when choosing between a roller feeder and an NC servo feeder to help you make an informed decision that aligns with your production requirements.
Differentiating Roller Feeder and NC Servo Feeder Technologies
Roller feeders and NC servo feeders represent two distinct technologies used in automated processing systems, each offering unique capabilities and benefits. Roller feeders rely on mechanical rollers to feed materials into processing equipment, providing a cost-effective and straightforward solution for basic feeding applications. On the other hand, NC servo feeders utilize advanced servo motor technology to precisely control the feeding process, offering higher accuracy, flexibility, and automation capabilities compared to roller feeders.
Factors to Consider When Choosing a Press Feeder Type
Precision and Accuracy
* Roller Feeder: While roller feeders are suitable for standard feeding tasks, they may lack the precision and accuracy required for complex or high-tolerance applications.
* NC Servo Feeder: NC servo feeders excel in delivering precise and accurate material feeding, making them ideal for demanding production environments that require tight tolerances and consistent part quality.
Flexibility and Versatility
* Roller Feeder: Roller feeders are relatively simple and easy to operate, making them suitable for applications with minimal changeover requirements and standard material sizes.
* NC Servo Feeder: NC servo feeders offer greater flexibility and versatility, allowing manufacturers to adjust feed lengths, speeds, and release angles to accommodate a wide range of materials and part geometries.
Automation and Integration
* Roller Feeder: Roller feeders are typically less automated than NC servo feeders, requiring more manual intervention and supervision during operation.
* NC Servo Feeder: NC servo feeders are highly automated and can be seamlessly integrated into advanced manufacturing systems, enabling lights-out operation and enhanced production efficiency.
Making the Right Choice for Your Production Needs
When deciding between a roller feeder and an NC servo feeder for automated processing, it is essential to evaluate your specific production requirements, material characteristics, and desired output quality. If precision, flexibility, and automation are paramount in your manufacturing operations, opting for an NC servo feeder may offer the best long-term benefits and performance enhancements. However, for simpler applications with lower accuracy demands, a roller feeder could provide a cost-effective solution to meet basic feeding needs.
Title
As the professional manufacturer of steel coil handling equipment, except for the decoiler machine, punch press, we also provide the topper press feeder. Surely, the nc servo feeder and roller feeder are included.
Conclusion
In conclusion, regarding the press feeder, the choice between a roller feeder and an NC servo feeder for automated processing hinges on a careful assessment of your production goals, operational requirements, and budget constraints. By weighing the advantages and considerations of each press feeder type, manufacturers can make an informed decision that optimizes efficiency, quality, and productivity in their automated processing workflows. Whether you prioritize precision, flexibility, or automation, selecting the right feeder technology is crucial for driving success and competitiveness in today's fast-paced manufacturing landscape.