Do You Know Progressive Stamping?
- Share
- Issue Time
- Dec 20,2024
Summary
Progressive stamping uses progressive dies to combine punching, bending, and forming into one efficient process. It ensures precision and cost-effectiveness...
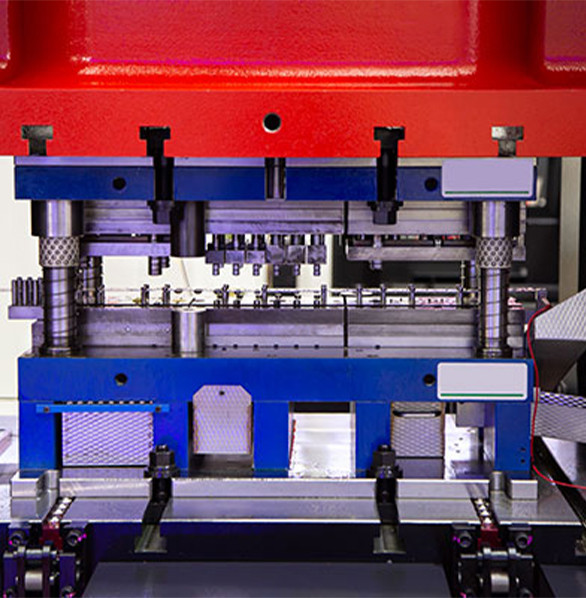
Progressive stamping is a cornerstone of modern manufacturing, leveraging the precision and versatility of progressive dies to transform raw materials into finished components in a seamless and efficient process. At the heart of this technology are progressive stamping dies, which integrate multiple operations—such as punching, bending, and forming—into a single, continuous production cycle. This makes the process ideal for industries requiring high-volume production, including automotive components, electronic connectors, and household appliance parts.
What Is Progressive Stamping?
Progressive stamping is a highly automated, multistage metalworking process designed for high-volume production. Imagine a strip of metal journeying through a series of stamping stations within a single die. At each station, a specific operation—such as punching, bending, or forming—is performed, gradually transforming the raw material into a finished product.
For instance, the automotive industry frequently uses progressive stamping to manufacture intricate seatbelt components. These parts demand precise cuts, bends, and assembly points, all of which are achieved through this streamlined process.
How Does It Work?
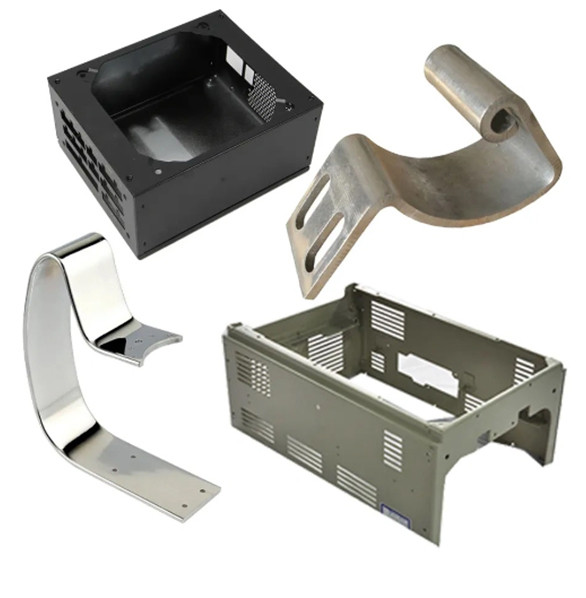
To better illustrate the progressive stamping process, let’s take the example of a metal terminal used in electronic circuits:
Material Feeding
A roll of copper or stainless steel is fed into the press using an automated servo feeder, ensuring exact alignment.
Initial Punching
At the first station, the die punches small holes that will later serve as connection points.
Forming Features
Subsequent stations bend tabs into precise shapes, while others coin specific features for conductivity and structural integrity.
Final Cut and Part Ejection
The last station trims the terminal from the strip, producing a fully functional part ready for assembly.
Why Choose Progressive Stamping?
Here’s why industries worldwide rely on progressive stamping:
Unmatched Efficiency
Progressive stamping can produce thousands—or even tens of thousands—of parts per hour. This speed makes it ideal for large-scale production lines like automotive safety systems or consumer electronics.
Cost Savings
By combining multiple operations into a single tool, manufacturers save on labor, tooling, and setup costs. For example, producing parts for household appliances like hinges or brackets becomes significantly more economical.
Superior Precision
CNC-controlled progressive presses deliver parts with tight tolerances, often as low as ±0.001 inches. This level of accuracy is essential in the medical industry, where components like surgical clips demand absolute precision.
Material Optimization
Progressive die design minimizes scrap, ensuring maximum material usage—a crucial factor for sustainability in today’s eco-conscious manufacturing world.
Applications
Automotive: Progressive stamping is used to manufacture seatbelt mechanisms, brake components, and engine brackets.
Electronics: Terminals, connectors, and battery contacts for smartphones and laptops.
Appliances: Structural parts like motor mounts and door hinges.
Case Study:
A leading automotive supplier used progressive stamping to produce a seatbelt latch component. By designing a die that integrated 8 different operations, they reduced production time by 30% and saved 20% on material costs compared to traditional stamping methods.
Challenges to Consider
While progressive stamping offers numerous advantages, it comes with its share of challenges:
Complex Tooling Design
Progressive dies must be meticulously engineered to ensure smooth material flow and avoid stress fractures. For instance, high-strength materials like titanium alloys demand specialized dies, which increase development time and cost.
Initial Investment
The upfront cost for progressive dies and high-tonnage presses can be significant, making it less accessible for small-scale operations.
The Future of Progressive Stamping
As industries push for greater efficiency and sustainability, progressive stamping is evolving in exciting ways:
Smart Manufacturing
IoT-enabled sensors embedded in stamping presses monitor performance in real-time, predicting maintenance needs and reducing downtime.
Advanced Materials
Lightweight yet durable materials like high-strength steels and aluminum alloys are becoming more common in aerospace and automotive industries, pushing the limits of die technology.
Green Manufacturing
Progressive stamping processes are being optimized to reduce energy consumption and maximize material usage, aligning with global sustainability goals.
Conclusion
Progressive stamping stands at the intersection of precision, efficiency, and innovation. Whether it's producing high-strength automotive parts or delicate electronic components, this technology has proven its value across industries. As advancements in materials, automation, and sustainability continue to shape the manufacturing landscape, progressive stamping is poised to remain a cornerstone of industrial production.
By understanding and leveraging the potential of progressive stamping, manufacturers can stay ahead of the curve—producing better products faster, cheaper, and with minimal environmental impact.