Why Investing in Stamping Press Automation is a Smart Choice for Manufacturers ?
- Share
- Issue Time
- Jan 20,2025
Summary
Stamping press automation improves productivity by integrating coil feeding and precision stamping technology. Explore how it can streamline production lines and lower operational costs effectively.
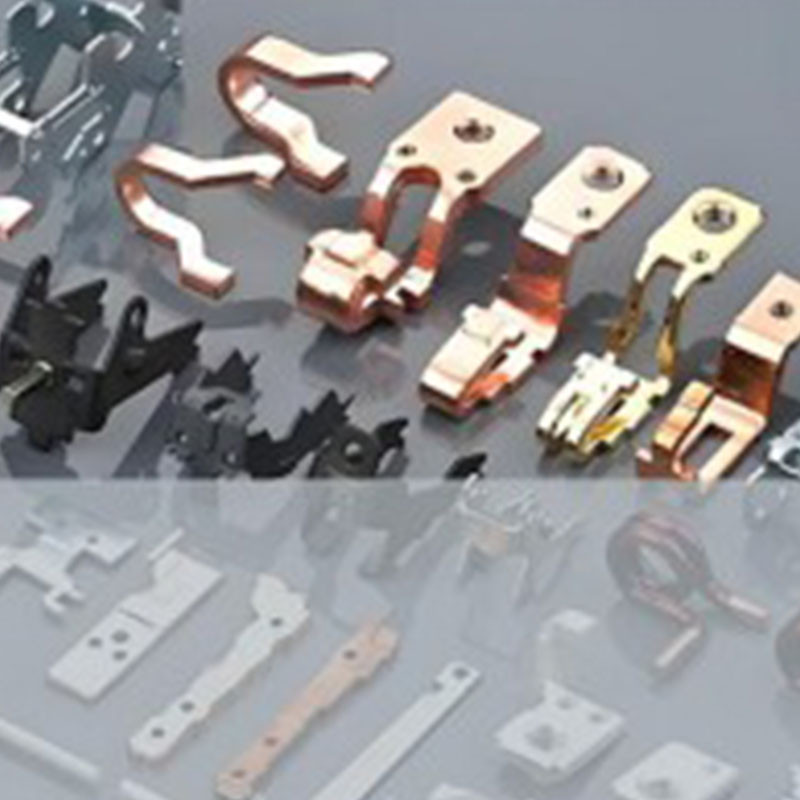
When it comes to modernizing manufacturing processes, stamping press automation solutions are indispensable. Coil feeding automation and advanced stamping equipment have been the cornerstone of progress in metal forming industries worldwide, offering manufacturers enhanced productivity and operational efficiency in precision stamping.
How Stamping Press Automation Works
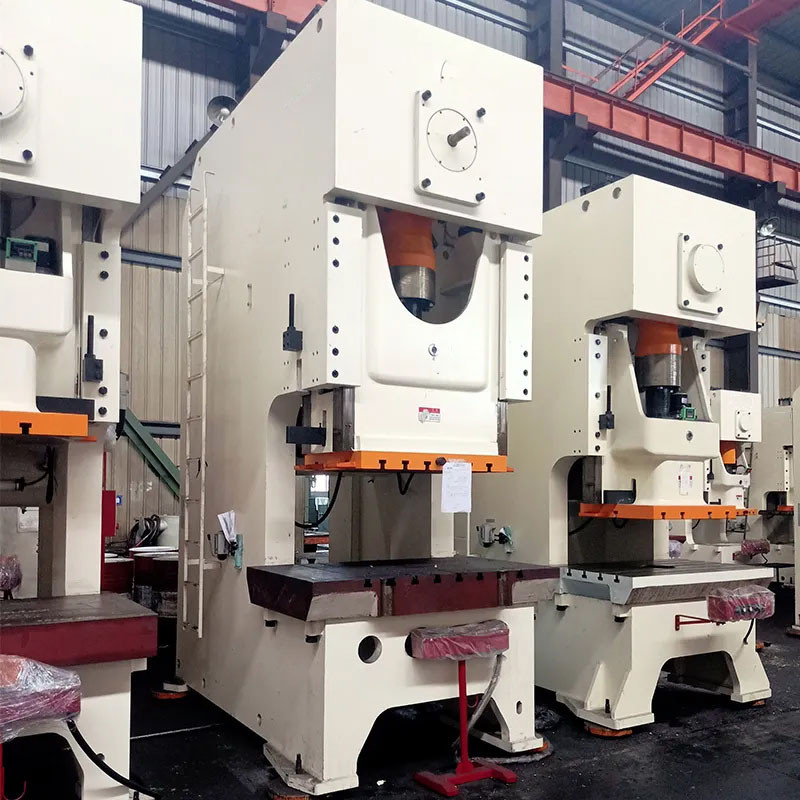
At the heart of any automated stamping line is the press automation system, which controls the application of force to shape and cut metal parts. By automating this process, manufacturers can increase speed, reduce the risk of human error, and ensure consistent part quality. The inclusion of automated coil handling systems ensures that material is fed into the press without delay, minimizing downtime and maximizing production time.
Advantages of Automated Stamping Lines
Investing in automated stamping systems offers numerous benefits, including reduced labor costs, improved part consistency, and quicker turnaround times. Additionally, integrating decoilers, feeders, and presses into a single system enables better coordination across the entire production line, improving overall efficiency.
Real-World Success Stories
In many industries, including automotive and electronics, stamping press automation has become the standard for high-volume production. Companies that have integrated automation solutions into their stamping lines have reported significant improvements in both production speed and part quality, leading to reduced production costs.
Conclusion
With the continuous advancements in metal stamping automation equipment, manufacturers are now able to meet the growing demands of the global market. Embracing press automation is no longer a luxury—it’s a necessity for staying competitive and efficient in today’s fast-paced manufacturing environment.